Your Reliable Electric Building Wire Supplier since 2000
Being a professional manufacturer of building wire over 20 years, we are able to provide you a package solution of the wire and its accessories, such as
- Aluminum or copper cable lug
- DIN Rails
- Copper Busbar
- LV circuit breaker
- Colorful Cable Tie
What is an Electric Building Wire
Building wire is composed of either solid or stranded aluminum or copper and is insulated with PVC, nylon, XLPE, or CPE sheathing. It is commonly used in commercial and industrial buildings to install new circuits or extend existing ones within walls and ceilings, typically installed in a conduit, cable tray, or raceway.
PowerTel & its associated factory can provide you a package supply of building wire and its accessories, like cable tie, cable lug, DIN Rail, cable tray & busway, LV circuit breakers etc.
Electric Building Wire by UL Standard
According to UL Standard, building wire types are, THHN, THWN, TFFN, XHHW,RHW/RHW-2 Building Wire.
Refer to UL 83 & 2256 Standard
Over PVC Insulation Nylon Jacketed
Color & Length on your request
Refer to UL 83 & 1581 Standard
Over PVC Insulation Nylon Jacketed
Wet condition less 75C
Solid or stranded CU Conductor
Refer to UL 66 & 758
RoHS & REACH Compliant
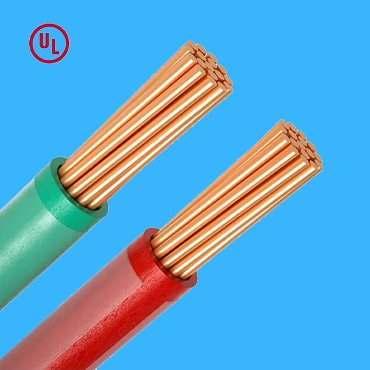
FR-XLPE Insulated with Nylon outer jacket, used in industrial & commercial areas, refer to UL 44 & VW1
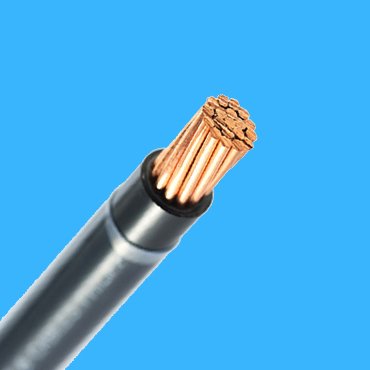
Underground Service Entrance cable installed in conduit or a direct burial.
Refer to UL 44, 854 & 1685
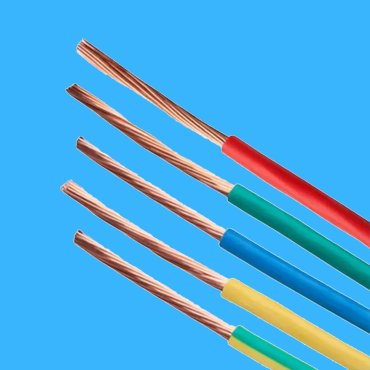
Rubber Insulated wire & cable can be used in wet locations.refer to NEMA WC70 or ICEA S-65-658
Electric Building Wire by IEC Standard
Building Wire by British Standard
Product Feature Box
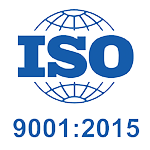
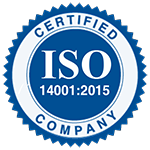
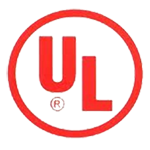
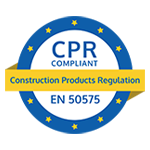
Ut semper ipsum ex, quis aliquet justo pretium a Ut semper
Our Dedicated Workman
Our most modern and advanced manufacturing facilities, as well as the dedication of our employees to ensure that each step in the manufacturing process is perfect.all these help to ensure that the highest quality of materials are used and building wire meets the highest standards.
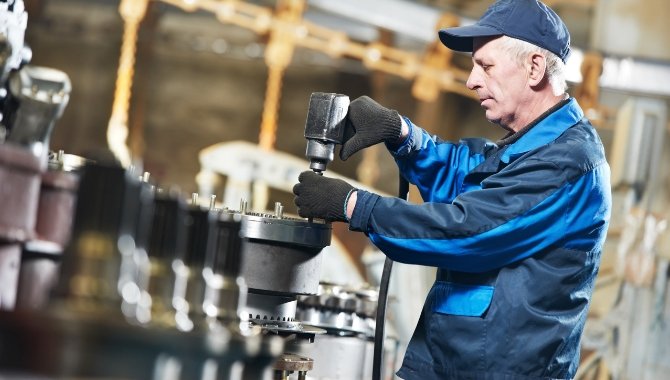
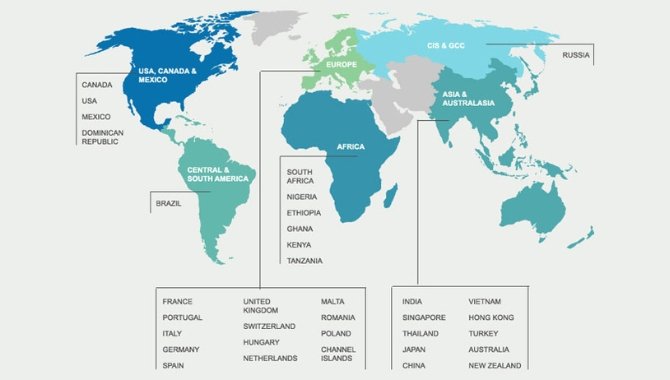
UL & CPR Certificated Building Wire
Most of our building wire are UL & CPR certificated seperately. this made us have a good sale throughout the world and receieved a brand recognition.
Package Supply of Building Wire & its accessories
Through years of experience, we have been dedicated to provide a package solution for our customers from the building wire itself and its accessories,, like cable lug, cable tie, DIN Rails, LV circuit breaker etc. One-stop buy will save your time & costs a lot.
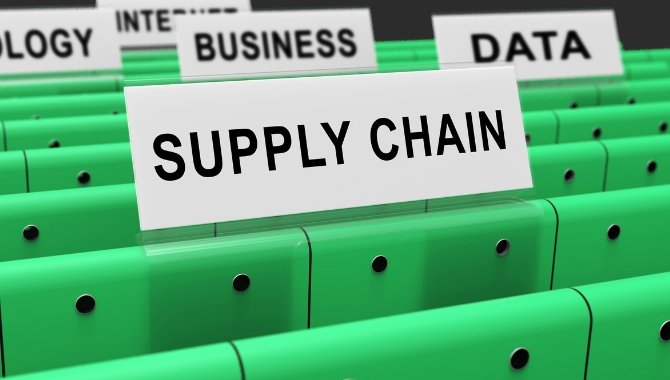
Related Product
Installation Guide for Building Wire
1. According to the manufacturer’s written instructions, applicable standard requirements, and recognized industry practices, lay wires, cables, and joints to ensure that the laying meets the requirements and can achieve the expected purpose.
2. Make necessary coordination to ensure proper connection of building wire to other projects.
3. If multiple building wires need to be laid in the same path and wires need to be pulled out at the same time.
4. Use anti jamming adhesive to connect the copper strip to the busbar.
5. Use adhesives or lubricants when necessary; The adhesive used should not corrode building wires or insulators.
6. Use pulling methods that do not damage building wires or channels, including retractable coils, cables, ropes, and square tissue wire/cable clamps.
7. Lay exposed building wire, parallel or rubber, or exposed to structural components, and lay along surface contours as appropriate.
8. Before pulling out the building wire, complete the laying of conduits or channels (tightly connected and ensuring the entire circuit).
9. Do not pull out thermoplastic wires when the temperature is below -170 ° C.
10. Secure the building wire at the upper end and intermediate joints of all risers in accordance with approved manufacturers and applicable electrical specifications.
11. If the building wire enter buildings from underground through conduits, use approved non hardening adhesive to seal the wires and conduits.
12. If required, install wire spacing devices. Provide conduit devices at the terminals to isolate the wires, including galvanized or cadmium plates, steel or malleable iron conduits, and devices and non-metallic insulation materials, with holes in appropriate locations to facilitate proper isolation of cables.
13. In some systems, equipment provided by approved manufacturers may require different wire quantities and arrangements than specified on the drawings. In this case, following this requirement will not result in any additional costs being borne by the owner.
14. Bundle and tie three-phase neutral (if used) conductors laid in conduits in wire paths and large pull out boxes to limit unbalanced load on the conductors.
15. All terminals and lighting equipment ends should be fully relaxed for connection and maintenance. Place the loose end in the outlet box.
16. Configure connectors at access boxes, control panel devices, pipe trays, terminal panels, etc., and provide materials compatible with building wires, insulators, and protective sheaths on wires.
17. Keep the quantity of conduit joints in a electrical system minimize as much as possible.
18. Install connectors with mechanical strength and insulation level equal to or higher than the connected building wires. Use connectors that are compatible with the wire material.
19. Strengthen the power joints and terminals according to the torque values published by the manufacturer, including screws and bolts. If there are no specified manufacturer’s torque requirements, connect the joints and terminals to meet the approved manufacturer’s specified tightening torque.
20. Connect power supply wires and equipment wires according to the written instructions and wiring diagrams of the equipment manufacturer. Match the wires of the power connector for proper contact between the power supply and the installed equipment.
21. A joint made of power insulation material with an insulation induction level equal to or higher than the connected wire.
22. Prepare building wires by cutting and peeling off the covering armor, sheath, and insulation layer to ensure the uniformity and appearance of the terminated building wires. Avoid cutting through connectors on wires. When peeling off the insulation layer, it is also important to avoid cutting copper wires. Use specially designed tools to cut the armor sheath.
23. Thermoplastic wires cannot be laid on the raised floor in the computer area.